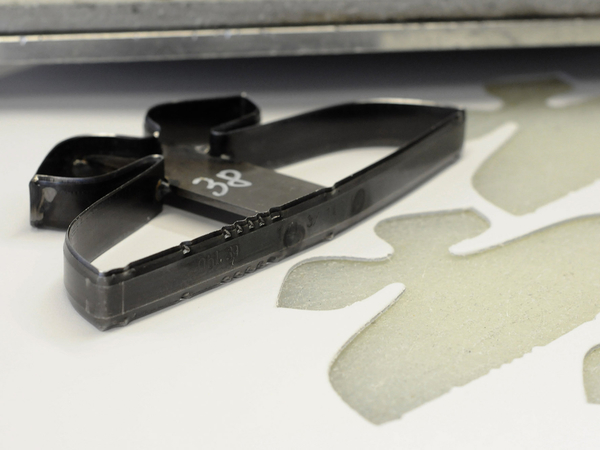
1. the punching of the handmade safety shoe
The individual shaft parts are cut to size with the help of punching knives. These have the exact shape of the individual stock parts and are made of steel ground on one or both sides. Notches, serrations and spikes are also worked in, which provide clues when the parts are later joined together.
2. sharpening the shoe
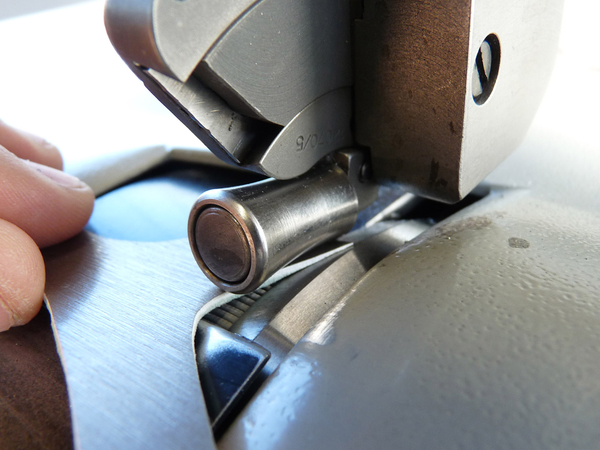
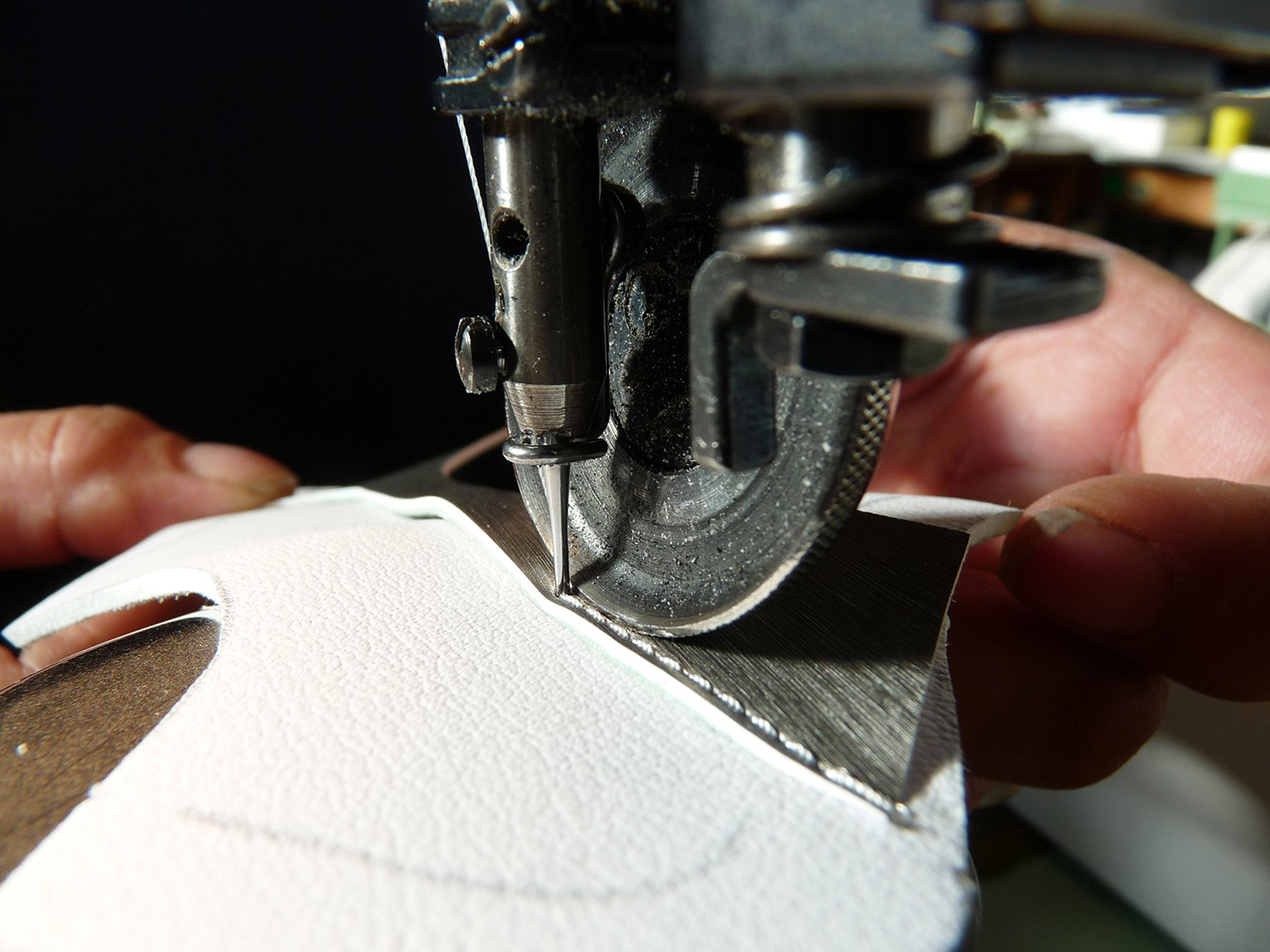
3. stitching the safety shoe
4. strobing
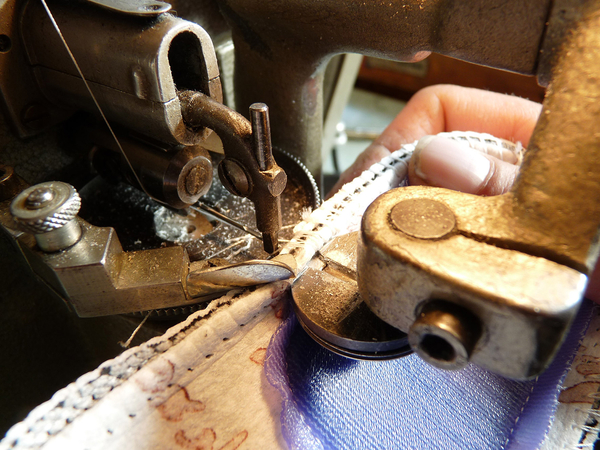
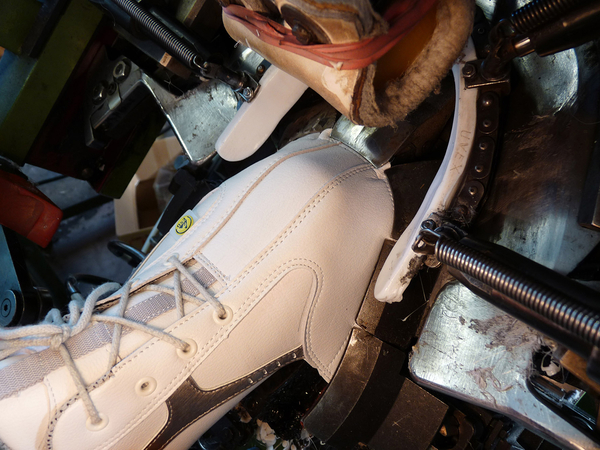
5. pinching
6. grind flat
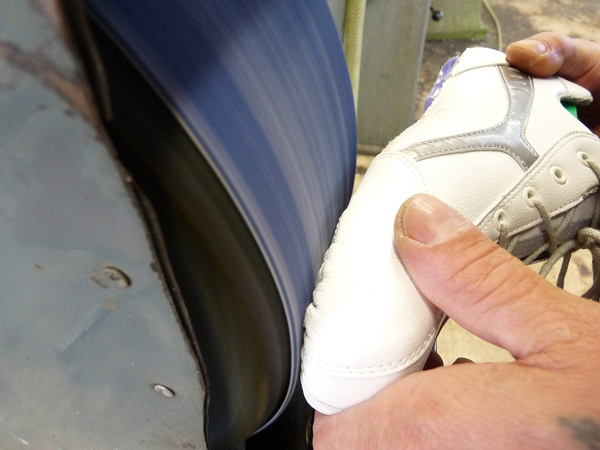
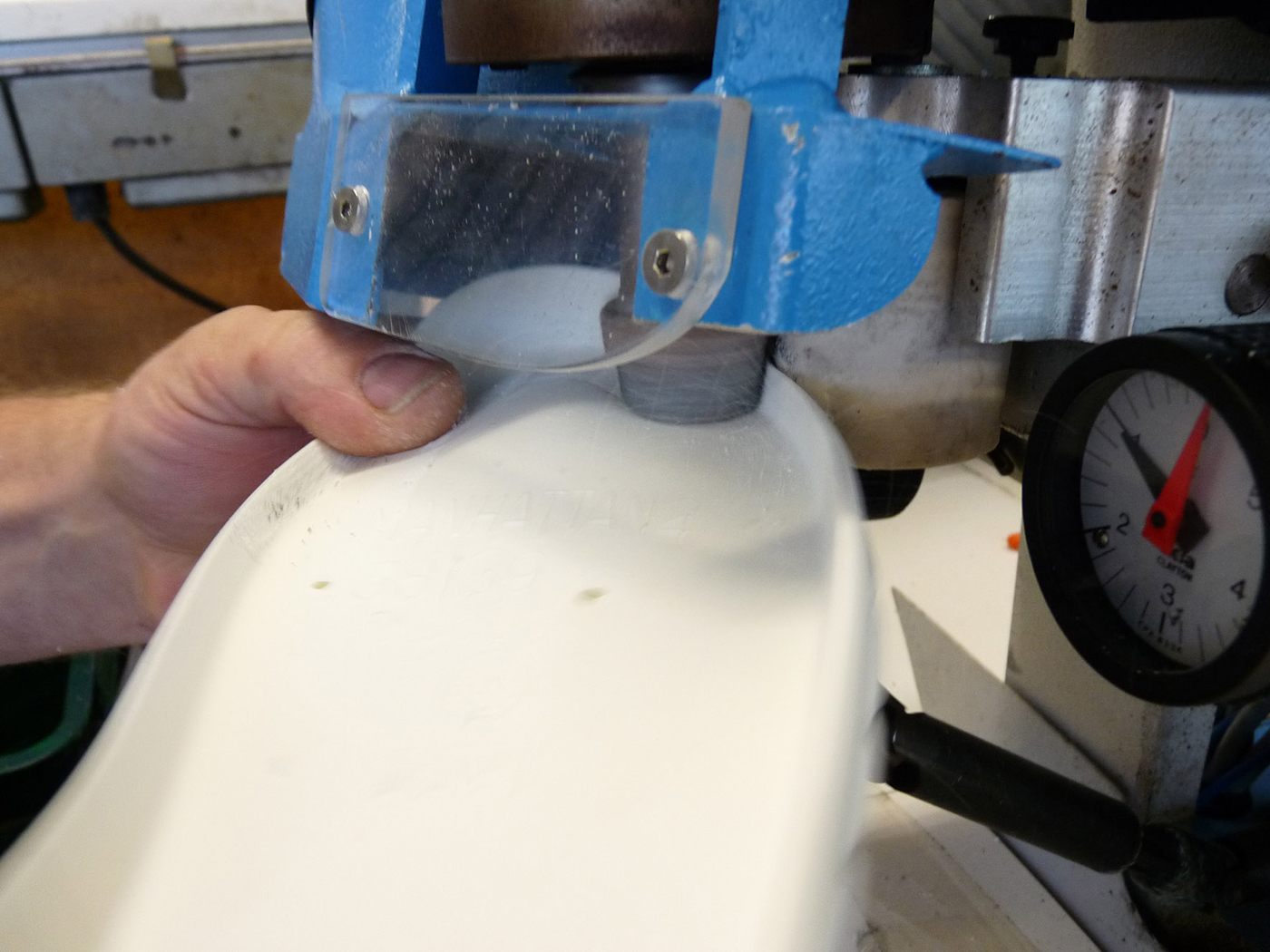
7. roughening
8. pre-drawing
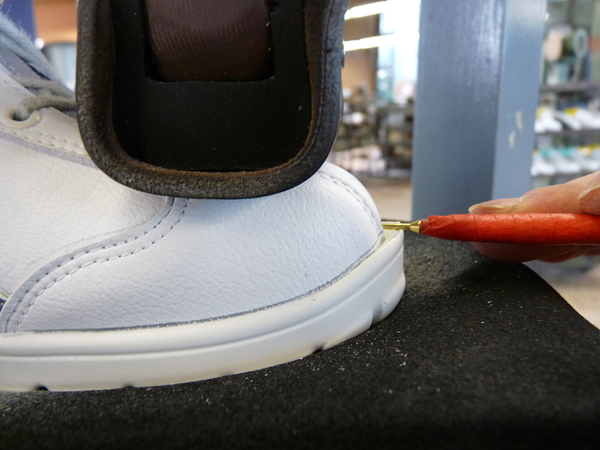
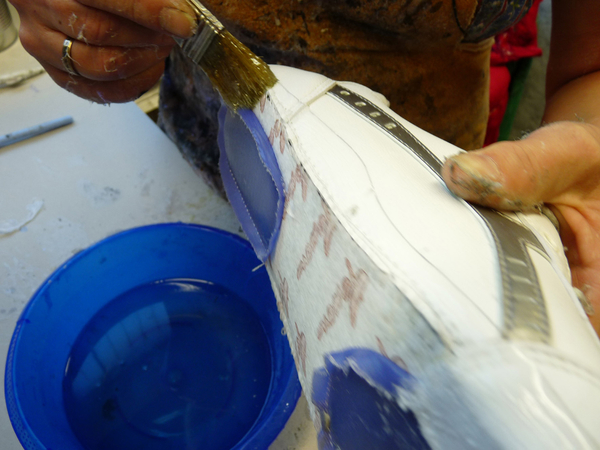
9. painting
10. placing the sole
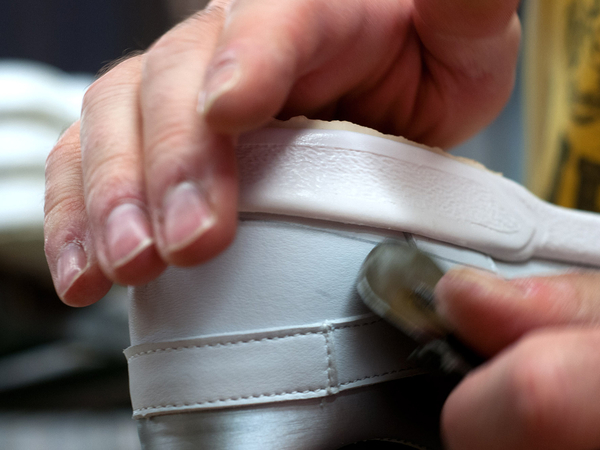
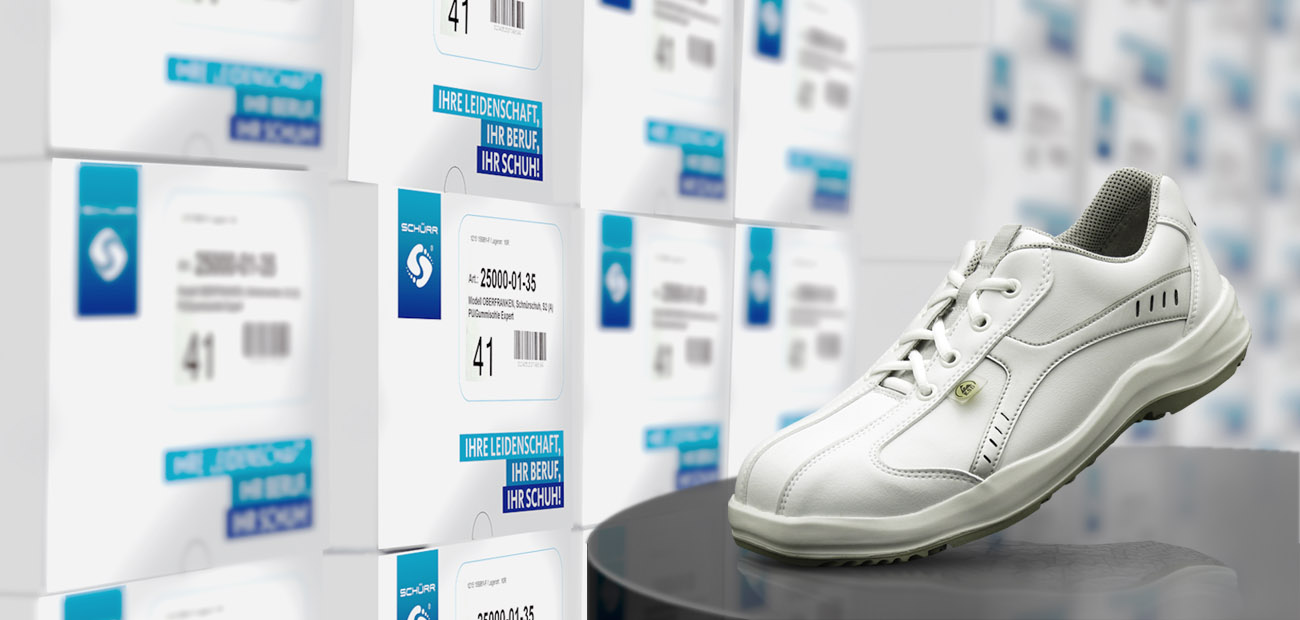